The Problem: A Hidden Threat to Critical Infrastructure
Eight years ago, Bryan Crowe, a Pipeline Operations Manager, found himself in a challenging situation in West Virginia. “I’m standing on top of a pipeline, looking down the right of way,” Crowe recalled, “and one of our pipeline technicians had done a locate and noticed a strange bend in the pipe.”
This pipeline was a critical piece of infrastructure, part of a network that fed one of the largest gas processing plants in the world. Shutting it down would have far-reaching consequences, potentially leading to a state of emergency in neighboring states and costing the company tens of millions of dollars daily.
The situation was perplexing because, despite the visible stress on the pipeline, there was no apparent evidence of a landslide—an event not uncommon in the region. “It was difficult to determine if the line had moved or if it was under stress from outside influences because there wasn’t really an evident landslide that had taken place,” Crowe explained.
The Dreaded Shut In: A Costly and Risky Intervention
“We can do our full integrity management program, run smart tools, have all the cathodic protection in the world, and still not detect this huge risk to our asset,”
Bryan Crowe
Without clear data to back their decision, the pipeline operator faced a difficult choice. “Out of an abundance of caution and the great safety culture that we had, we decided to shut the line in,” Crowe said. The team began to remove soil from around the pipeline, and it quickly became apparent that the pipe was moving—a sign of a significant problem.
The situation required an urgent and extensive intervention. “We ended up having to replace some 1,200-1,500 feet of right of way. Completely rebuilt the right of way, all the way down to the toe,” Crowe recounted. The team had to replace all three pipelines in that right of way, a massive effort completed in just ten days. “It was a huge cost to us, our producer customers, as well as consumers of the energy in that region,” Crowe noted, emphasizing the impact of the shutdown.
The Search for a Better Way: Identifying the Gaps in Data

This experience exposed a critical gap the pipeline operator’s pipeline integrity management strategy—relying solely on traditional monitoring methods left the company vulnerable to unseen threats. “We can do our full integrity management program, run smart tools, have all the cathodic protection in the world, and still not detect this huge risk to our asset,” Crowe reflected.
The Solution: Teren’s Geo Intelligence Suite

Recognizing the need for better data and a more proactive approach, Crowe approached Teren to conduct a case study using Teren’s Geo Intelligence Suite. “We wanted to see how many [geohazards] they could capture. Are they going to miss any? Can they see stuff that we can’t see?” Crowe explained.
The results were eye-opening. Teren’s intelligence prioritized 246 slips across a 300-mile stretch of MPLX’s critical pipelines—12 of which had gone undetected by traditional methods. “We were able to repair a lot of these landslides and slips and potential slip areas before they turned into a catastrophic failure,” Crowe said.
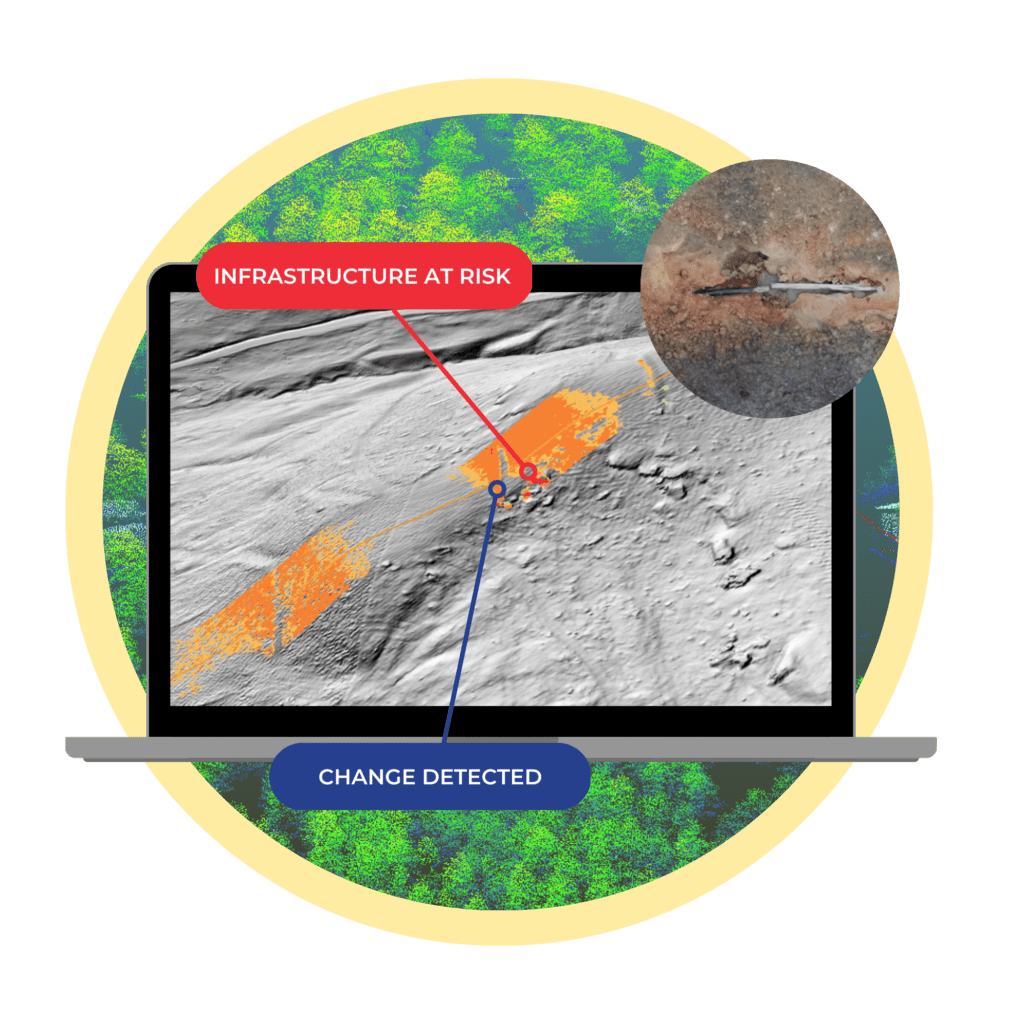
By switching from a reactive to a proactive maintenance program, the pipeline operator was able to reduce their average annual shut-ins from 3-5 to zero, cutting repair costs by nearly 90%. “We were really able to drive that cost down. Now you get a crew going and you can go and hit 50 sites for just $10,000 a slide to go out and re-divert some water or put a drain tile in,” Crowe elaborated.
The Results: A Maintenance Program that Funds Itself
“The avoidance of one major geohazard effectively funded our entire maintenance program,”
Bryan Crowe
The partnership with Teren not only improved the operator’s ability to detect and mitigate geohazards, but also revolutionized their overall approach to pipeline integrity management. “These programs really increased the safety of our assets and our people because we weren’t having people go out and walk these mountains all the time,” Crowe noted.
Teren’s technology allowed the company to transition from a reactive stance to a proactive maintenance strategy, significantly enhancing safety, reducing costs, and ensuring the continuity of critical energy supply. “The avoidance of one major geohazard effectively funded our entire maintenance program,” Crowe concluded.
How can Teren help you?
We'd love to hear from you.
- Ready to dive deeper? -
Knowledge Hub
White Papers
Webinars